Hexagonal Wire Mesh Products Supplier
We produce high-quality hexagonal wire netting, specifically gabion boxes used for river channel and river bank reinforcement, chicken wire garden fences, and poultry netting. Our hexagonal wire mesh is made of stainless steel and galvanized steel, available in various specifications, sizes, and finishes. We also accept customer customization and OEM orders.
Main Metallic Hex Mesh Products
Our products can be divided into three categories: Hexagonal Wire Netting, Poultry Netting and Chicken Wire. Poultry Netting and Chicken Wire are mainly hex mesh products for agricultural and farming uses. In the category of Hexagonal Wire Netting, we mainly introduce hex wire used in construction reinforcing, riverbank protection and fencing.
Material
Hexagonal Weave Wire Mesh is made commonly from low-carbon steel wire, galvanized or PVC-coated, stainless steel, or copper plated wire is also available for customers specific requirements.
Mesh Size
Hexagonal Wire Netting can be supplied in mesh opening from 1/2 inch to 4 inches. Poultry Netting typically has 1-inch or 2-inch mesh, while Chicken Wire usually has a 1-inch mesh.
Wire Diameter
Hexagonal Wire Netting is produced with a mesh wire diameter of 0.5 mm to 1.5 mm. Poultry Netting wire diameter 0.7 mm to 1.2 mm, Chicken Wire with a wire diameter 0.8 mm to 1.2 mm.
Weaving Method
Weaving method applied for hexagonal pattern wire mesh includes: Straight twist, reverse twist, triple twist, double twist, 5 twist.
Applications
Hexagonal Wire Netting is used for chicken wire, poultry netting, also gabions retaining wall, fencing and plaster reinforcement.
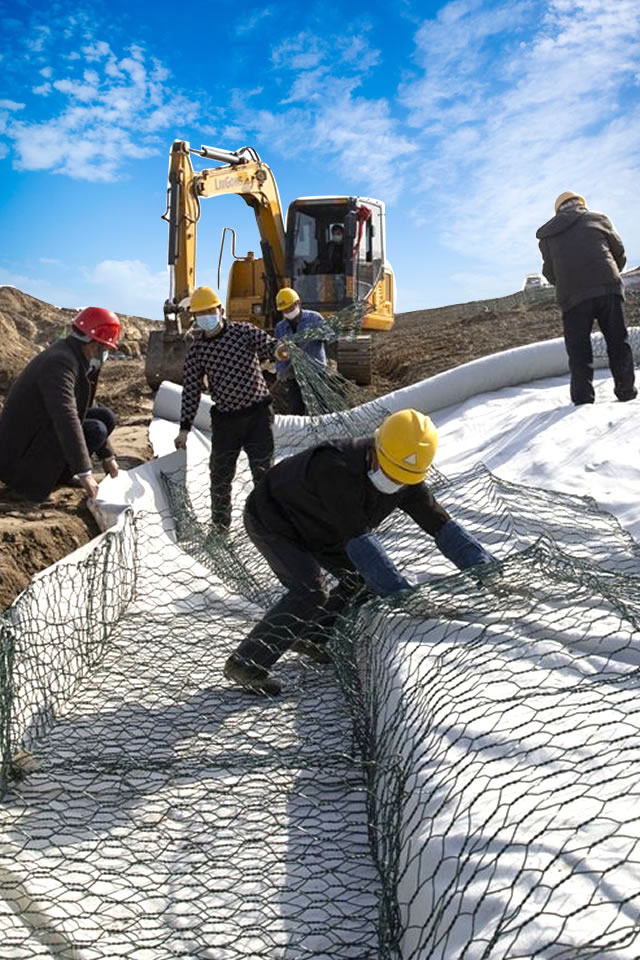
Hexagonal Weave Galvanized Steel Wire Mesh and Major Application
Hexagonal twist woven galvanized iron wire mesh can be galvanized or PVC coated galvanized. Finishes can be Hot-dip galvanized before or after weaving. Heavy type hexagonal wire mesh is mainly used for gabions retaining wall, shoreline protetion, light type hex wire is mainly used for light fencing and other uses.
Hex Chicken Wire Products We Supply
We supply hexagonal chicken wire in stainless steel 304, 316, and galvanized steel, with green PVC and black vinyl coating options. Chicken wire is popularly used for agriculture, gardening and crafts.ย
Supplied in two forms:
Mesh rolls for chicken wire fencing;
Mesh panels for egg layer cage system.
Customized Specifications
Welcome to cooperate
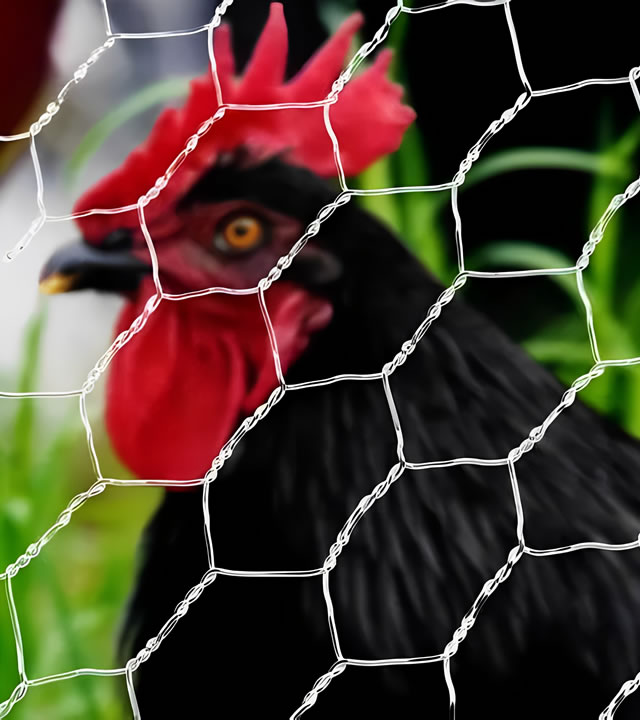
Chicken Wire of Various Materials
Simply send an email and we will give you a professional answer.
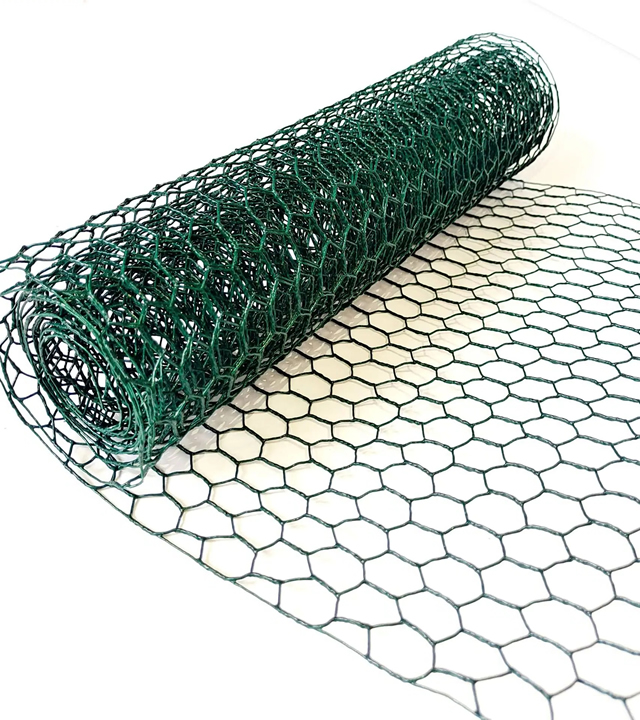
Garden Poultry Netting
25' X 50' 20-Gauge Garden Netting Poultry Netting Dark Green Powder Coated.
Supplying Durable, Weather-Resistant Poultry Netting
We offer various poultry netting fencing solutions, including Hexagonal Poultry Fence, Rabbit Hutch Netting, Poultry Yard Fencing, Welded Wire Poultry Fence, Duck Pen Netting, and Garden Poultry Netting. Our wire mesh products are used for poultry secure fencing and enclosures. Poultry netting materials we supply can be flexible hexagonal woven or welded wire mesh with enhanced strength.